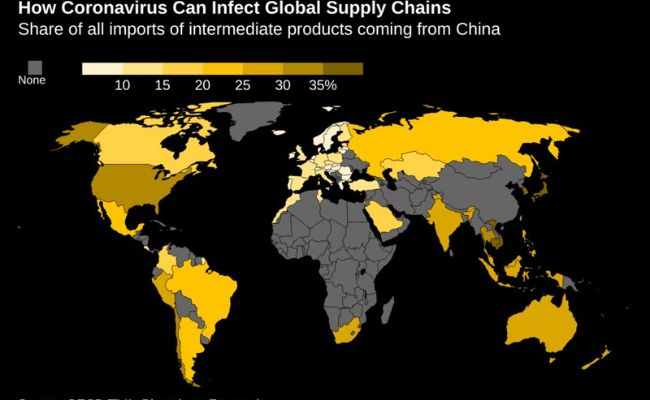
Executive Summary
The COVID-19 pandemic exposed significant vulnerabilities in global supply chains, causing widespread disruptions across industries. This case study focuses on a leading automotive manufacturer that faced severe challenges during the pandemic, including supply shortages, logistical bottlenecks, and delayed production schedules.
The disruption led to increased costs, reduced output, and strained relationships with suppliers and customers. The company responded by adopting a multi-faceted strategy, including diversification of suppliers, adoption of digital supply chain technologies, and a shift toward more localized production models.
This case study examines the root causes of the disruptions, the solutions implemented, and the outcomes achieved. It highlights the importance of resilience, flexibility, and digital transformation in mitigating supply chain risks and provides actionable recommendations for businesses to build more robust supply chains.
Introduction
Supply chain disruptions are a major risk for global businesses, particularly those operating in industries with complex and interconnected value chains, such as automotive, electronics, and consumer goods. The COVID-19 pandemic created unprecedented challenges, including factory shutdowns, labor shortages, transportation disruptions, and fluctuating demand.
This case study focuses on a leading automotive manufacturer that relied heavily on global suppliers and just-in-time (JIT) inventory practices. During the pandemic, the company faced disruptions in the supply of critical components, such as semiconductors, leading to production delays and financial losses. The task for the company was to stabilize its supply chain, minimize production delays, and adopt long-term strategies to enhance resilience against future disruptions.
Definition of Key Terms
1. Supply Chain Disruption: Any event that interrupts the normal flow of goods, services, or information in a supply chain.
2. Just-in-Time (JIT): An inventory management strategy where materials are ordered and received only as needed for production, minimizing inventory costs.
3. Resilience: The ability of a supply chain to recover quickly from disruptions and adapt to changing conditions.
4. Digital Supply Chain: The use of technology to enhance visibility, efficiency, and decision-making across the supply chain.
5. Localization: The strategy of sourcing and producing goods closer to end markets to reduce dependency on global supply chains.
The Problem
Challenges Faced by the Company:
1. Component Shortages: The pandemic caused shutdowns of key suppliers, particularly in Asia, resulting in a shortage of essential components like semiconductors.
2. Logistical Bottlenecks: Transportation disruptions, including port congestion and limited air cargo capacity, delayed shipments and increased costs.
3. Demand Volatility: Fluctuations in customer demand made it difficult to forecast and plan production schedules.
4. Dependency on Single Suppliers: Heavy reliance on a limited number of global suppliers for critical parts increased the company’s vulnerability.
5. Production Delays: The inability to source components on time led to significant delays in manufacturing, impacting revenue and customer satisfaction.
The Solution
To address these challenges, the company implemented a comprehensive set of measures:
1. Diversification of Suppliers:
- Identified and onboarded additional suppliers in different geographic regions to reduce dependency on a single source.
- Built relationships with local suppliers to enhance supply chain flexibility and reduce lead times.
2. Adoption of Digital Supply Chain Technologies:
- Implemented real-time tracking systems to improve visibility into inventory levels and shipment statuses.
- Leveraged AI and machine learning for demand forecasting and supply chain risk assessment.
- Used blockchain technology to enhance transparency and traceability across the supply chain.
3. Shift Toward Localization:
- Increased sourcing of components and materials from domestic suppliers.
- Established new manufacturing facilities closer to key markets to minimize transportation risks.
4. Improved Inventory Management:
- Shifted from a strict JIT model to a hybrid approach, maintaining strategic safety stock for critical components.
- Created buffer inventories at regional distribution centers to ensure continuity of supply during disruptions.
5. Strengthened Supplier Relationships:
- Collaborated closely with suppliers to understand their risks and support their recovery efforts.
- Introduced supplier diversification policies and joint contingency planning initiatives.
The Results
Quantitative Outcomes:
1. Reduced Production Downtime: Production downtime decreased by 50% within six months of implementing the new strategies.
2. Cost Savings: The adoption of digital supply chain technologies reduced logistics costs by 15%.
3. Faster Recovery: Time to recover from disruptions was reduced from 12 weeks to 6 weeks due to improved resilience measures.
4. Improved Supplier Base: The number of active suppliers increased by 30%, enhancing flexibility and reducing dependency on single sources.
Qualitative Outcomes:
1. Enhanced Visibility: Real-time tracking and AI-driven analytics improved decision-making and reduced uncertainty.
2. Increased Customer Satisfaction: On-time delivery rates improved, restoring customer confidence in the company’s reliability.
3. Stronger Relationships: Collaborative efforts with suppliers fostered mutual trust and long-term partnerships.
Limitations
1. Initial Costs: The transition to a more resilient supply chain required significant upfront investments in technology, infrastructure, and supplier onboarding.
2. Implementation Challenges: Adopting digital technologies and training employees posed logistical and technical difficulties.
3. Complex Coordination: Managing a diversified supplier base required enhanced coordination and communication.
4. Global Dependencies: While localization reduced some risks, the company remained partially dependent on global suppliers for specialized components.
Conclusion
The pandemic highlighted the vulnerabilities of global supply chains and underscored the need for resilience and flexibility. This case study illustrates how the automotive manufacturer addressed supply chain disruptions through strategic diversification, digital transformation, and localization.
Although the solutions required substantial investments and coordination, they yielded significant benefits, including reduced downtime, cost savings, and improved customer satisfaction. The company emerged from the crisis with a more robust and adaptive supply chain, better positioned to withstand future disruptions.
This case demonstrates that proactive risk management, technology adoption, and collaboration are critical to building resilient supply chains capable of navigating an uncertain global environment.
Discussion: Major Problems Summarized
1. Global Dependencies: Reliance on international suppliers increased vulnerability to disruptions.
2. Transportation Delays: Logistical challenges caused significant delays and higher costs.
3. Unpredictable Demand: Fluctuations in demand complicated production planning and inventory management.
4. Supply Chain Visibility: Lack of real-time data hindered effective decision-making during the crisis.
Recommendations / Key Learnings and Takeaways
1. Diversify Supply Chains: Reduce dependency on single suppliers or regions by building a more diverse supplier base.
2. Adopt Digital Technologies: Invest in AI, blockchain, and real-time tracking systems to enhance visibility and risk management.
3. Localize Production: Establish regional manufacturing hubs to minimize transportation risks and lead times.
4. Maintain Strategic Inventory: Adopt a hybrid inventory model with safety stock for critical components.
5. Strengthen Collaboration: Work closely with suppliers to identify risks and develop joint contingency plans.
6. Prepare for Uncertainty: Incorporate scenario planning and stress-testing into supply chain management to anticipate and mitigate future disruptions.
References
1. Chopra, S., & Meindl, P. (2023). Supply Chain Management: Strategy, Planning, and Operation. Pearson.
2. World Economic Forum. (2023). The Resilient Supply Chain Report.
3. Deloitte Insights. (2024). Digital Supply Chains: The Future of Resilience.