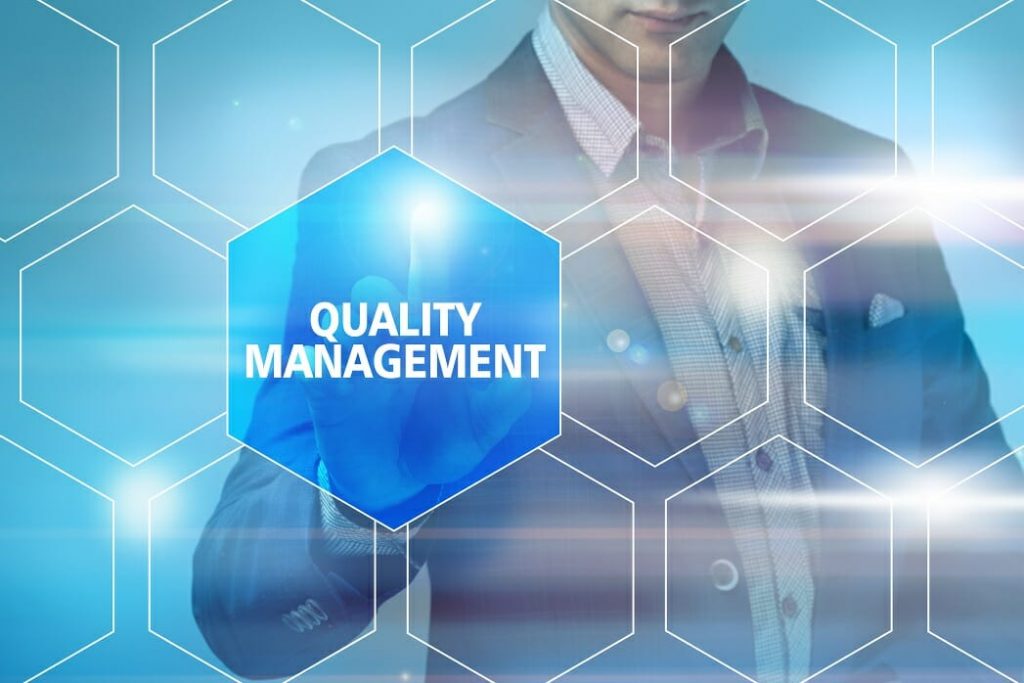
Quality management systems (QMS) have been in place since the beginning of the Industrial Revolution. They were used to manage and curtail defects in products and eventually evolved to become a set of standards that controlled both the product and production processes.
As manufacturing and production lines became more automated and accelerated in the 1950s and ’60s, and production rates increased rapidly, quality became even more important because the potential of large quantities of sub-standard products entering the market became a reality. Quality control (QC) systems eventually gave way to quality assurance (QA) systems when manufacturers began to understand that quality products had to have quality built into the production process, and not just a QC system that discovered defects in an end item inspection and scrapped bad parts.
Evolution of the QMS market
The QMS market focuses on modern QMS systems that represent the evolution of quality management to its current portfolio of products. Today, a comprehensive portfolio of quality systems would include audit management, compliance management, corrective and preventive actions (CAPA), defect tracking, document management, feedback tracking, incident management, non-conformance tracking, risk management, and supply chain quality. Some QMS providers focus on specific areas such as SPC, quality assurance assessment, and enterprise quality consulting.
The QMS market sectors are divided between PLM, MES, and ERP suppliers that offer QMS systems as a part of their overall enterprise software portfolio. Most MES products offer quality management as an integrated component of an overall manufacturing planning and execution portfolio. Some of the large PLM providers offer MES as a component of their design/build/operate lifecycle. Most of the current QMS market are pure play QMS providers, many representing point solutions that focus on specific quality technologies.
Today, the term that describes the market is QMS, where TQM (Total Quality Management) refers primarily to the underlying methodology and approach to the quality process. Perhaps the most common description of how quality and quality improvements have evolved into present-day QMS is the identification of: Quality Inspection, Quality Control, Quality Assurance, and TQM.
From quality control to quality assurance
The quality inspection stage began about the same time (early 20th century) that large manufacturing and mass assembly production lines emerged. Companies like Ford, then one of the world’s largest manufacturers, employed teams of inspectors to check the quality of the model-T car. Some elements of statistical quality control were introduced in the 1930s and ’40s, but this method of quality control was the primary process until the 1970s and ’80s when quality assurance emerged from the Japanese auto manufacturers.
The quality assurance (QA) phase focuses on pre-production processes and relies on quality standards (most notably ISO 9000) or instructions to assist with reduction of the risk of failures and mistakes in the processes used to produce a product or service. ISO 9000 is now used extensively throughout the world as the de facto guide to quality assurance.
The fourth stage, TQM, involves understanding and implementing quality management principles and concepts in every aspect across the organization and enterprise from product design to manufacturing to customer feedback. TQM is focused on continuous process improvement procedures in which all organizations of the enterprise are involved and committed to quality as a mindset and process. In other words, the quality is built into the enterprise and overall process, assuring a quality product.
QMS extends beyond manufacturing
Overall growth in the QMS software market will be driven primarily by the demand for more reliable products by consumers in emerging markets. One of the major trends in this market is the rapidly growing sales of goods over the internet that will require producers to offer quality products that will not be returned, as processing these returns due to quality issues represents a major cost center for internet-based sales.
While quality assurance and overall continuous improvement methods have been in place for decades in discrete manufacturing, the adoption of these quality methods have moved to other industries like bio-tech/pharma, medical devices, consumer goods and services, and non-manufacturing industries like power generation and utilities, financial and banking services, consumer goods, and food & beverage. Additionally, the QMS market now includes technologies focused on occupational safety and environmental and sustainability issues, further expanding the reach of the quality assurance space.